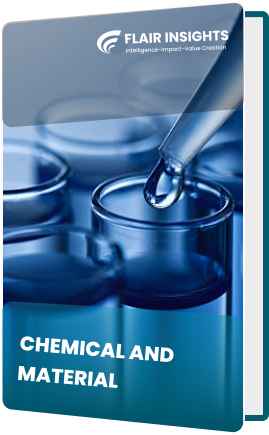
Global Metal Foams Market By Type (Aluminum, Nickel, Copper), By Application (Automotive, Medical, Industrial), By Region, And Segment Forecasts, 2023 to 2032
Report Id: 44162 | Published Date: May 2024 | No. of Pages: 10 | Base Year for Estimate: May 2024 | Format:
The global metal foams market is witnessing significant growth, driven by the increasing demand for lightweight, durable, and high-performance materials across various industries. Metal foams are a class of porous materials with a cellular structure, made from metals such as aluminium, titanium, and nickel. The manufacture of medical equipment is one of the primary applications for metal foams. One important factor driving the market is the rise in demand for these medical devices. Furthermore, increasing the usage of metal foams in heat exchangers will quicken market growth.
The global metal foam market was valued at USD 0.9 billion in 2024 and is projected to reach to USD 0.116 billion by 2032, exhibiting a growth rate of 3.64% during the forecast period 2024-2032. Sustainability is a key factor influencing demand for metal foams, especially aluminium foams. Aluminium foams are produced from recycled materials and do not contain any foam-stabilizing chemicals. These components support the affordability and eco-friendliness of the materials. Revenue from the global metal foam market is increasing as a result of the increased use of aluminium foams in wall cladding, lighting fixtures, terrazzo flooring, and showroom displays.
Premium Insights:
Growing investments in research and development are leading to the development of new metal foam products with enhanced properties and functionalities.
Advances in manufacturing technologies, such as additive manufacturing and powder metallurgy, are enhancing the production capabilities and expanding the applications of metal foams.
Global Metal Foams Market Dynamics:
Drivers: Versatility of metal foams, growing adoption in additive manufacturing and increased usage and demand in transportation and aerospace
Metal foams can be produced from various metals and with varying pore sizes and distributions. This allows for tailoring their properties to specific applications, offering engineers design flexibility.
The increasing use of additive manufacturing (3D printing) for metal components opens doors for the integration of metal foams into complex designs. This can lead to lighter and more functional parts.
The increasing focus on fuel efficiency and emissions reduction in transportation and aerospace sectors drives demand for lightweight materials. Metal foams offer exceptional strength-to-weight ratios, making them ideal for weight reduction in vehicles and aircraft structures.
Restraints: High production costs, limited availability of standardised products, technical challenges, fluctuations in raw material prices
Manufacturing metal foams can be a complex and high-cost process compared to traditional metals. This limits their widespread adoption in cost-sensitive applications.
The relative novelty of metal foams means there are fewer standardised product variants available compared to conventional metals. This can pose challenges for design engineers seeking readily available options.
Joining and machining metal foams require specialised techniques due to their unique structure. This can increase manufacturing complexity and potentially raise production costs.
The prices of metals used to manufacture metal foams can fluctuate significantly. This can impact the overall cost and market stability.
Opportunities: Development of application-specific metal foams, standardised and certification and focus on sustainability and lightweighing
Research and development efforts focused on creating metal foams with targeted properties for specific applications (e.g., high-temperature resistance, specific acoustic dampening) can unlock new market opportunities.
Establishing standardised product specifications and certification processes for metal foams can boost confidence in their performance and reliability, encouraging wider adoption.
The growing emphasis on sustainability and lightweight materials in various industries, such as automotive and construction, creates a favourable environment for the adoption of metal foams.
Market By Metal Foams Market Insights:
Based on material type, the market is segmented into Aluminum, Copper, Nickel, and Zinc. The copper segment dominates the market due to strong anti-corrosion properties, high energy resistance, and strong conductivity. This material's electromagnetic shielding and noise absorption properties make it useful in a variety of applications. It is mainly used as a buffering material in pressure-reducing devices that use pressure gauges. It also aids in the absorption of vibrations, thermal insulation, and other beneficial materials.
Based on product type, the market is segmented into open-cell and closed-cell. The category with the highest revenue generation was closed-cell metal foam. Closed-cell foams allow liquids and air to pass through them. Thickness, improved coefficient of friction, and tear resistance are expected to have a major impact on the market for closed-cell foam. These cells can perform a greater range of tasks than open-cell foams. The use of closed-cell foams is expanding because they are more resilient and pressure-tolerant than open-cell foams.
Market By End Use Insights:
Based on the end-use industry, the metal foam market is segmented into three categories: automotive, bio-medical, and marine. The category that brought in the most revenue was automobiles. Because of their excellent performance and lightweight, metal foams are becoming more and more common in the manufacturing of lightweight cars. Concerns about greenhouse gas (GHG) emissions are another factor contributing to the automotive industry's widespread use of metal foams. Transportation contributes significantly to carbon dioxide emissions, especially personal vehicles.
Market By Region Insights:
Based on regional coverage, the global metal foams market is segmented into North America, Europe, and Asia-Pacific. The Asia-Pacific region is expected to have the largest market share in the metal foam market in 2024 due to the presence of significant market players such as ERG Aerospace Corp., Admatis Ltd., Alantum, CYMAT Technologies Ltd., and Armacell, among others. Additionally, rising metal foam utilisation in the automotive sectors of many nations, particularly China, is boosting market revenue development.
Competitive Scenario:
Major players in this region include ERG Aerospace Corporation, CYMAT Technologies Ltd Aluminum King Co. Ltd, Alantum, Ultramet, Mott Corporation, Mayser GmbH & Co. KG, among others
Scope of Work: Global Metal Foams Market
Key Market Developments
March 2021- Mott, a pioneer in the development of flow control and filtration systems for a range of markets, including semiconductor, medical, and industrial, has partnered with Banner Industries. High-performance, versatile fluid control devices are ideal for many important filtration and flow applications. In addition to those tools, Mott also makes a range of gas flow restrictors, gas diffusers for quick vent applications and purifiers that clean process gases.
October 2022- ERG Aerospace Corporation announced the expansion of its production facilities to meet the growing demand for aluminum foams in the automotive and aerospace industries. The expansion aims to increase production capacity and enhance product quality.
July 2023- CYMAT Technologies Ltd. launched a new line of composite metal foams with enhanced thermal and acoustic insulation properties. The new product line is targeted at the building and construction industry to improve energy efficiency and reduce noise pollution.
Frequently Asked Questions (FAQs)
What are the key drivers of the global metal foams market?
Ans Key drivers include the Versatility of metal foams, growing adoption in additive manufacturing and increased usage and demand in transportation and aerospace
Which regions are leading the adoption of metal foam technologies?
Ans Asia Pacific is the leading region in the Global Metal Foams Market driven by technological advancements, lower production costs, and industrial innovation that is driving market expansion.
What are the main challenges faced by the metal foams market?
Ans. Challenges include high production costs, limited availability of standardised products, technical challenges, fluctuations in raw material prices
What are the emerging opportunities in the metal foams market?
Ans. Emerging opportunities include the development of application-specific metal foams, standardised and certification and focus on sustainability and lightweighing

Speak with an analyst to get exclusive insights tailored to your needs